Das Beschichten von Massenartikeln (Schüttgut) erfolgt meist im Tauch–Schleuder–Verfahren. Dabei ist der Korb bzw. die Tauchtrommel mit einem Durchmesser von 400–900 mm das wichtigste Werkzeug. Das Schüttgut wird in den Korb geladen. Die Füllhöhe ist von der Schüttdichte der Teile abhängig. Je nach Tauch-Schleuderparameter und Lackeinstellung kann pro Beschichtungsvorgang eine durchschnittliche Schichtdicke von 3–6 μm aufgebracht werden.
Bei einigen speziellen Bauteilgeometrien (Kraftinnenangriffe, Kleinstteile, Hinterschneidungen) ist für die vollständige Oberflächenbenetzung ein Schwenken des Korbes ratsam. Gleiches gilt für das Abzentrifugieren von überschüssigem Beschichtungsmaterial nach der Benetzung. Ein Neigungswinkel von ≥ 75° bei einer Drehzahl von etwa 5–20 U/min ermöglicht ein verbessertes Auslaufen von überschüssigem Beschichtungsmaterial. Dies kann mit einem Vorschleudern vor dem Kippprozess kombiniert werden.
Anschließend wird der Korb in den Tauchbehälter getaucht. Der Lack benetzt die gesamte Oberfläche der Teile. Eine mechanische Bewegung durch langsames Drehen des Korbes verbessert den Benetzungsprozess, indem Blasen entfernt und die Kontaktflächen verändert werden.
Nach dem Tauchvorgang wird der Korb aus dem Tauchbad gehoben und schnell gedreht bzw. zentrifugiert, so dass die beschichteten Teile an die Außenwand des Korbes geschleudert werden. Durch die Fliehkraft tropft der überflüssige Lack durch die Löcher des Korbes zurück in den Tauchbehälter. Nach der Beschichtung müssen die Teile im Ofen getrocknet werden. Dabei empfiehlt es sich, die Teile beim Ausleeren der Trommel auf ein Förderband oder in eine Kiste (Horde) möglichst weit voneinander zu verteilen. Dadurch werden ein besserer Einbrennprozess, ein geringeres Aneinanderhaften und eine gleichmäßigere Qualität der Beschichtung erreicht.
Der Prozess des Tauch-Schleuderns wird durch mehrere Parameter beeinflusst. Die wichtigsten sind Eintauchdauer, Schleudergeschwindigkeit, Schleuderdauer und Beladung sowie Viskosität des Lackes. Daneben gibt es noch weitere Parameter, die sich auf den Prozess auswirken. Diese hängen von der Beschichtungstechnik ab, wie etwa das Schwenken der Schleudereinheit und/oder Richtungsänderung, was zu einer Qualitätsverbesserung führen kann.
Empfohlene Parameter: Die Eintauchdauer des Korbes in den Lack muss mindestens 30 Sekunden betragen. Eine geringe Drehgeschwindigkeit von etwa 10–20 U/min und ein oszillierendes Eintauchen verbessert die Benetzung, anhaftende Bläschen können so entfernt werden.
Ein wichtiger Parameter ist die Schleudergeschwindigkeit bzw. Fliehkraft (F), die sich aus der Drehgeschwindigkeit und dem Trommeldurchmesser ergibt.
Die Fliehkraft errechnet sich wie folgt: \( F = m \omega^2 d / 2 \)
m = Masse eines Tropfens Lack (nahezu konstant)
d = Durchmesser
\(\omega\) = Winkelgeschwindigkeit (\(\omega 2 \pi n/t\))
n/t = Umdrehungen je Zeiteinheit (z. B. U/min/60)
Die Formel:
\( F = m \left(2 \pi \times \frac{n_1}{60}\right)^2 \times \frac{d_1}{2} = m \left(2 \pi \times \frac{n_2}{60}\right)^2 \times \frac{d_2}{2} \)
\( \Rightarrow n_1^2 \times d_1 = n_2^2 \times d_2 \)
\( \Rightarrow n_2 = n_1 \times \sqrt{\frac{d_1}{d_2}} \)
Korbdurchmesser (\( d_1 \)) = 900 mm, Drehgeschwindigkeit (\( n_1 \)) = 219 U/min
Umrechnung auf Korbdurchmesser (\( d_2 \)) = 500 mm, Drehgeschwindigkeit (\( n_2 \))?
\( n_2 = 219 \, \text{U/min} \times \sqrt{\frac{900 \, \text{mm}}{500 \, \text{mm}}} = 294 \, \text{U/min} \)
Um mit einem kleinen Korb ein in etwa vergleichbares Beschichtungsergebnis zu erzielen, ist die Drehgeschwindigkeit zu erhöhen. Für ein Korb mit 500 mm Durchmesser muss die Drehgeschwindigkeit z. B. auf 294 U/min gesteigert werden.
Korbdurchmesser [mm] | Drehzahl [rpm] |
---|---|
300 | 380 |
400 | 329 |
500 | 294 |
600 | 268 |
700 | 248 |
800 | 232 |
900 | 219 |
1000 | 208 |
Die Schichtdicke hängt von der Schleudergeschwindigkeit und dem Korbdurchmesser ab: je höher die Schleudergeschwindigkeit und je größer der Korbdurchmesser, desto geringer das Schichtgewicht bei gleicher Viskosität.
Die Schleuderdauer beträgt pro Schleuderrichtung etwa 10–20 Sekunden. Für gewöhnlich wird jeweils nach rechts und nach links abgeschleudert. Je nach Geometrie der zu beschichtenden Teile kann dieser Vorgang wiederholt werden.
Neben dem Korbdurchmesser hat auch die Konstruktion (Geometrie) des Korbes einen Einfluss. So müssen geschlossene Ausführungen z. B. mit geringerer Lochdichte oder Doppelwand mit an- gepassten Parametern zentrifugiert werden.
Außerdem führen die Menge der Teile und die Beschleunigung des Schleudervorgangs zu einer unterschiedlichen Flussgeometrie (siehe Abbildung 12). Ein idealer Materialfluss wird in den Trommeln a) und b) erzielt. Beide Trommeln weisen vergleichbare Eigenschaften auf, da der Abstand der Teile, durch den der Lack fließen muss, gleich ist. Bei zu hoher Beladung oder einer geringen Beschleunigung ergeben sich beim Schleudern Korbfüllungen wie bei c) und d). Es ist offensichtlich, dass der Lack in Trommel c) den längsten Weg zurücklegen muss (siehe blauer Pfeil). Hier ist ein Anhaften der Teile untereinander aufgrund der Klebewirkung des Lackes wahrscheinlich. Außerdem ergeben sich in Trommeln c) und d) ungleichmäßige Schichtgewichte. In der Mitte liegende Teile haben ein größeres Schichtgewicht (aufgrund der geringeren Beschleunigung) als am Rand liegende Teile.
Darüber hinaus kann das Schichtgewicht durch die Viskosität des Lackes beeinflusst werden. Je niedriger die Viskosität, desto weniger Lack bleibt auf der Bauteiloberfläche haften. Die Viskosität ist an die Bauteilgeometrie und das Anlagenkonzept anzupassen. Für lösemittelbasierte Basecoats wird ein Startwert zwischen 40 und 42 Sekunden empfohlen (Richtwerte siehe technisches Merkblatt).
Zunächst erfolgt eine Probebeschichtung, um das Schichtgewicht zu beurteilen und zu überprüfen, ob die Kundenanforderungen damit erfüllt werden.
Wenn die Anforderungen nicht erfüllt werden, müssen die Schleuderparameter angepasst werden: Schleudergeschwindigkeit, Schleuderzeit, Viskosität und Füllmenge im Korb.
Wie in Kapitel „3.3. Viskosität“ beschrieben, wird die Viskosität eines Lackes von der Temperatur, der Lösungsmittelverdunstung und dem Festkörper beeinflusst. Daher ist für eine konstante Temperatur des Lackbehälters zu sorgen, um eine gleichbleibende Qualität sicherzustellen. Auf die Badtemperatur können folgende Umstände Einfluss nehmen: wechselnde Tag- und Nachttemperaturen, abgestrahlte Ofenwärme, warme Bauteile und Klimaschwankungen.
Daraus folgt die Festlegung, Kontrolle und Einhaltung eines konstanten Viskositätsfensters (festgelegte Verarbeitungsviskosität ± 2 Sekunden). Im Allgemeinen besteht ein Systemaufbau aus mehreren Schichten. Zwischen den einzelnen Beschichtungszyklen werden die Teile von dem Korb in den Ofen transportiert und wieder zurück. Schütt- und Transportprozesse verletzen die Beschichtung. Daher ist dieser Vorgang auf ein Minimum zu beschränken.
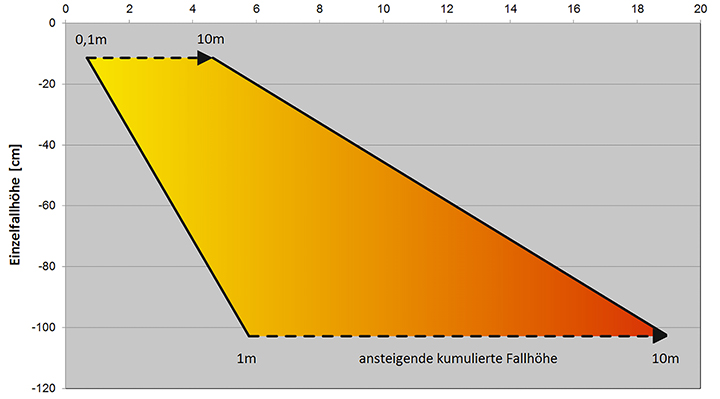
Die Teile sollten schonend auf das Vortrocknungsband vom Ofen oder in die Horde entladen werden. Mechanische Belastungen können zu signifikanten Beschädigungen der Beschichtungen führen und damit die Korrosionsschutzwirkung verringern.
Je größer die Teile und je größer die Fallhöhe, desto größer der Schaden. Ein Gummi oder Kunststoffbelag auf dem Boden oder das Verringern der Fallhöhe durch Rutschen mit einer entsprechenden Neigung können deshalb hilfreich sein. Zusätzliche Belastung bzw. Beschädigungen der Bauteile können durch Vibrationsrinnen oder einem Ausschleusen der Bauteile nach jedem Beschichtungsgang verursacht werden.
Ein wichtiger Aspekt bei erneut zu beschichtenden Teilen ist deren Temperatur. Die Teile müssen auf ≤ 30 °C abgekühlt werden, aber noch oberhalb der Taupunkttemperatur liegen, bevor sie wieder beschichtet werden. Da Basecoats und Topcoats unterschiedliche Lösungsmittel enthalten, müssen getrennte Körbe und Tauchbehälter verwendet werden. Wenn die falschen Lösungsmittel in den Lack gemischt werden, kann dieser geschädigt werden.
Die regelmäßige Reinigung (Entlackung) der Beschichtungskörbe in ausreichend kurzen Abständen ist zwingend erforderlich, da Lackaufbau und das Zusetzen (Verkleben) der Körbe die Qualität der Beschichtung, Schichtdicke und deren Verteilung entscheidend beeinflussen kann. Mögliche Verfahren sind: Nass-chemisch, thermisch, mechanisch oder auch mittels Laser.
Kommentare (0)
Noch keine Kommentare.
Haben Sie konstruktives Feedback?
Bitte Einloggen um einen Kommentar zu hinterlassen.