7. PROZESSBEGLEITENDE PRÜFUNGEN
Um die bestmögliche Qualität einer Beschichtung zu ermöglichen, sind vor, während und nach dem Beschichtungsvorgang eine Vielzahl von prozessbegleitenden Prüfungen erforderlich.
Lack | Bauteil | Umgebung | |
---|---|---|---|
vor der Beschichtung | Temperatur, Viskosität, Festkörpergehalt, Füllstand | Sauberkeit | Temperatur, Luftfeuchtigkeit, Taupunkt |
während der Beschichtung | - | ||
nach der Beschichtung | - | Benetzung, Schichtgewicht (Schichtdicke), Haftung, Reibungszahl, Korrosionsschutz | - |
Die folgenden Kapitel beschreiben die Vorgehensweise dieser prozessbegleitenden Prüfungen. Weitere Informationen im Kapitel 10: Kontrollpläne.
Die in diesem Handbuch und in den technischen Merkblättern angegebene Viskosität bezieht sich stets auf eine Temperatur von 20 °C (DIN 53211 - 3mm). Die Viskosität hängt in großem Maße von der Temperatur des Beschichtungsmaterials selbst ab, daher gehört zu jeder Viskositätsmessung die Dokumentation der Temperatur. Das übliche Messverfahren wird mit einem Auslaufbecher, der in verschiedenen Formen erhältlich ist, durchgeführt (siehe technisches Merkblatt).
Zunächst muss das Material durch Mischen homogenisiert werden, bevor eine Probe entnommen wird.
Der zweite Schritt ist die Temperaturmessung mittels Thermometer und anschließender Dokumentation.
Drittens ist die Zeit zu messen, die der Lack benötigt, um aus dem Becher zu fließen. Jede Messung ist mindestens durch eine zweite Messung zu verifizieren.
Bei Verwendung eines Bechers mit Stativ:
- Bedecken Sie das Auslaufloch mit der Fingerspitze.
- Füllen Sie den Becher.
- Bedecken Sie den gefüllten Becher mit einer Glasplatte.
- Nehmen Sie Ihren Finger vom Auslaufloch.
- Ziehen Sie die Glasplatte zügig beiseite und starten Sie die Stoppuhr.
- Stoppen Sie die Stoppuhr, sobald der Lackfluss unterbrochen wird.
Bei Verwendung eines Tauchauslaufbechers wird gewöhnlich direkt aus dem Lackbehälter gemessen:
- Tauchen Sie den Becher in den Behälter.
- Ziehen Sie ihn zügig heraus, halten ihn senkrecht und starten Sie die Stoppuhr.
- Stoppen Sie die Stoppuhr, sobald der Lackfluss unterbrochen wird.
In beiden Fällen ist zu überwachen, dass sich am Auslauf keine Blasen bilden. Ist dies der Fall, ist die Messung zu wiederholen. Der Auslaufbecher ist nach jeder Messung gründlich zu reinigen (mit Pinsel und geeigneter Verdünnung, nicht mechanisch).
Benötigte Materialien: Auslaufbecher, Stoppuhr, Mischer, Thermometer.
Ein Qualitätscharakteristikum von Lacken ist das Verhältnis von flüssigen zu festen Bestandteilen. Zu den Feststoffen zählen die Bindemittel und Pigmente (Bestimmung gemäß DIN EN ISO 3251). Die Trocknungszeiten und Temperaturen sind dem jeweiligen technischen Merkblatt zu entnehmen.
Zunächst muss das Material durch Mischen homogenisiert werden. Anschließend folgt:
- Wiegen der leeren Schale (mleer).
- Entnehmen einer Lackprobe (ca. 1 g) und Befüllen der Schale.
- Erneutes rasches Wiegen der Schale (mvorher), um ein Verdunsten der Lösungsmittel zu vermeiden.
- Einbringen der Schale in den heißen Ofen.
- Entnehmen der Schale nach der angegebenen Zeit und auf Raumtemperatur abkühlen lassen (am Besten in einem Exsikkator).
- Erneutes Wiegen der Schale (mnacher).
Der Feststoffgehalt wird anhand folgender Formel ermittelt:
% Festkörper = (mnach Einbrennen mit Probe - mleer) / (mvor Einbrennen mit Probe - mleer) * 100 %
Hilfsmittel: leichte Schale (Aluminium), Laborwaage (Messgenauigkeit: ± 0,001 g), Ofen, Stoppuhr, Pipette, Exsikkator
Es stehen auch vollautomatische Geräte zur Verfügung (siehe Anhang C „Empfohlene Messgeräte und Prüfeinrichtungen“). Ergebnisse dieser Geräte können von der oben beschriebenen Methode abweichend sein. Entscheidend ist, dass immer nach derselben Methode gemessen wird, um vergleichbare Ergebnisse zu erhalten.
Der Taupunkt ist die Temperatur, bei welcher sich die Luftfeuchtigkeit auf einer Oberfläche niederschlägt (kondensiert). Sie ist abhängig von der Luftfeuchtigkeit und der Lufttemperatur.
Beträgt die Lufttemperatur beispielsweise 30 °C und die Luftfeuchtigkeit 55 %, so wird sich auf einer Oberfläche, dessen Temperatur 20 °C oder weniger beträgt, die Feuchtigkeit aus der Luft kondensieren (siehe Abbildungen 18). Da Zinklamellen-Basecoats extrem wasserempfindlich sind, muss die Lacktemperatur in jedem Fall mindestens 3 °C über der Taupunkttemperatur liegen. Eine Tabelle zum Ablesen der Taupunkttemperatur befindet sich im Anhang. Gelangt Wasser in das zinklamellenhaltige Beschichtungsmaterial, so wird es irreparabel geschädigt. Die im Lack enthaltenen Bindemittel reagieren bei Wasserzugabe ähnlich wie Zement. Es entsteht eine zähflüssige Masse, welche nach einiger Zeit sogar vollständig erstarren kann (siehe Abbildung 19 und 20).
Die Taupunkttabelle befindet sich im Anhang Tabelle 11
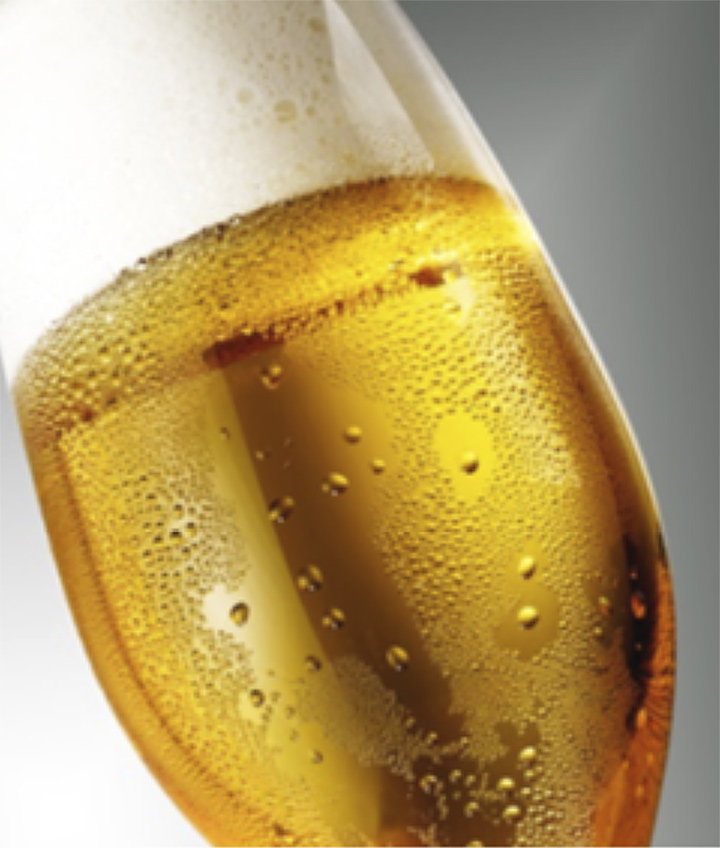
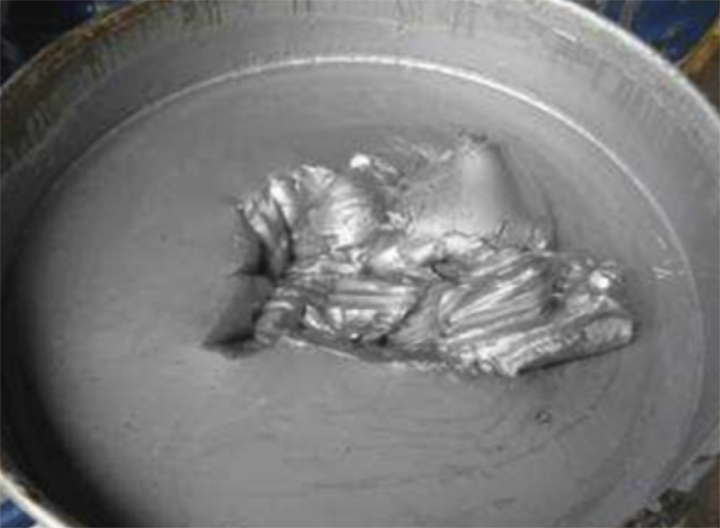
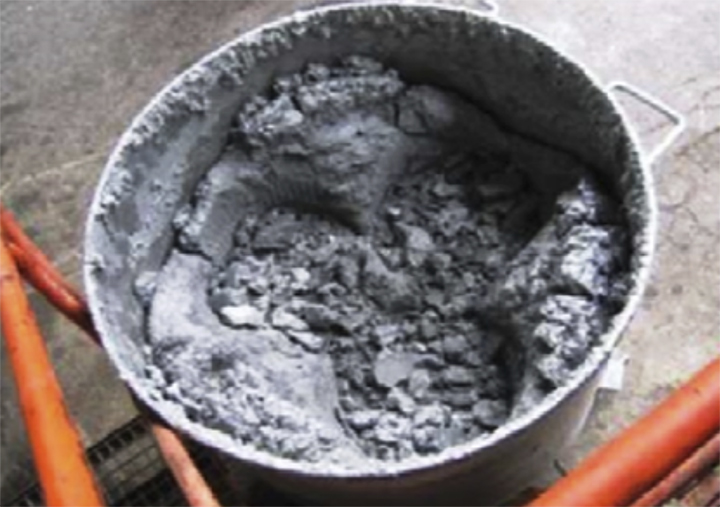
Für alle Eigenschaften von Oberflächen gibt es analytische Verfahren. Da diese sehr aufwendig sind, dienen die hier beschriebenen Prüfungen nur als Hilfsmittel, um im Vergleich mit optimalen Referenzbauteilen eine Bewertung vornehmen zu können. Das Vorgehen ist hierbei immer intern zu standardisieren.
Diese Prüfungen beschreiben keine systemrelevanten Freigabeprüfungen für den Endkunden. Da der Beschichtungsprozess einer Vielzahl von Einflüssen unterliegt, ist das Beschichtungsergebnis regelmäßig zu überwachen.
Die notwendigen Prüfungen müssen gemäß den Qualitäts-Managementrichtlinien eingeführt und validiert werden. Hierbei sind die erforderlichen Prüfintervalle zu definieren. Jedes Los muss nach statistischen Richtlinien geprüft werden.
Mit diesem Test kann die Sauberkeit der Substratoberfläche überprüft werden. Auf einer blanken Stahloberfläche erzeugt eine Kupfersulfatlösung eine sichtbare, chemische Wechselwirkung (festhaftender Kupferniederschlag), die nur stattfindet, wenn das Substrat frei von Rückständen, wie z. B. Öl, Fett oder Zunder, ist (siehe auch Anhang D „Test auf Versiegelung – Verfahren: Tüpfeltest“).
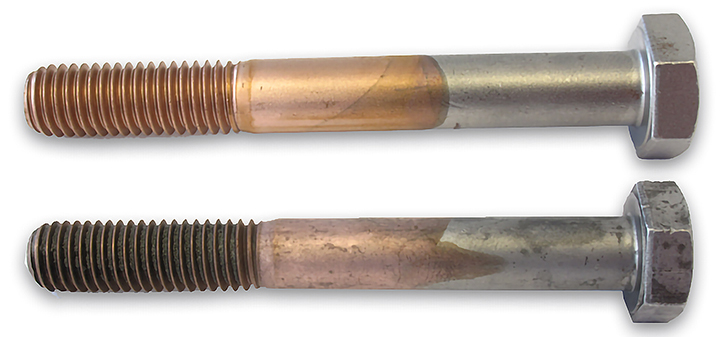
Je größer die gemessene Oberflächenspannung ist, desto sauberer ist das Substrat. Die Spannung wird mithilfe mehrerer Testtinten bestimmt. Für einen Beschichtungsprozess können interne Referenzwerte bestimmt werden, die ein Mindestmaß an Sauberkeit beschreiben.
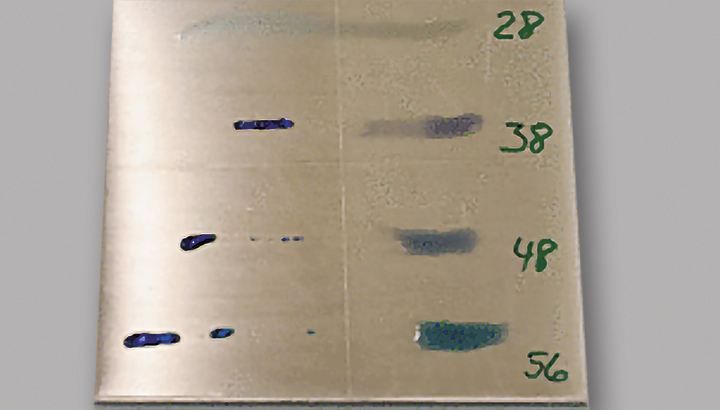
Bei diesem Test werden Wassertropfen auf die Oberfläche aufgetragen. Je fettiger/öliger die Oberfläche ist, desto prägnanter steht der Wassertropfen auf der Oberfläche. Eine deutliche Tropfenbildung lässt auf eine unreine Oberfläche schließen.
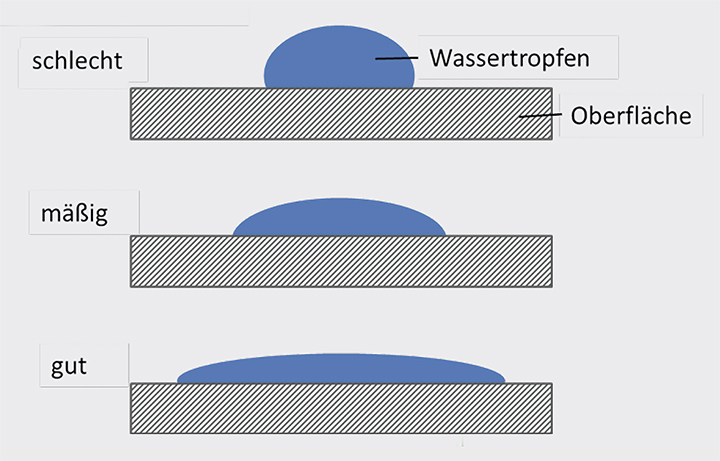
Ein zuvor gereinigtes Bauteil wird in einen mit kleinen Keramikkugeln (Zirblast® B60: 0,125–0,25 mm) gefüllten Behälter getaucht. Danach wird das Bauteil vorsichtig entnommen und 2 mal leicht gegen eine feste Oberfläche geklopft. Im Anschluss wird bewertet, ob noch Keramikkugeln an der Oberfläche des Bauteils anhaften. Bei noch anhaftenden Keramikkugeln ist das Ergebnis als n.i.O zu bewerten. In Abwesenheit von Keramikkugeln auf der Oberfläche des Bauteiles ist das Ergebnis als i.O. zu bewerten. Der Test ist mit stets neuen sauberen Keramikkugeln durchzuführen.
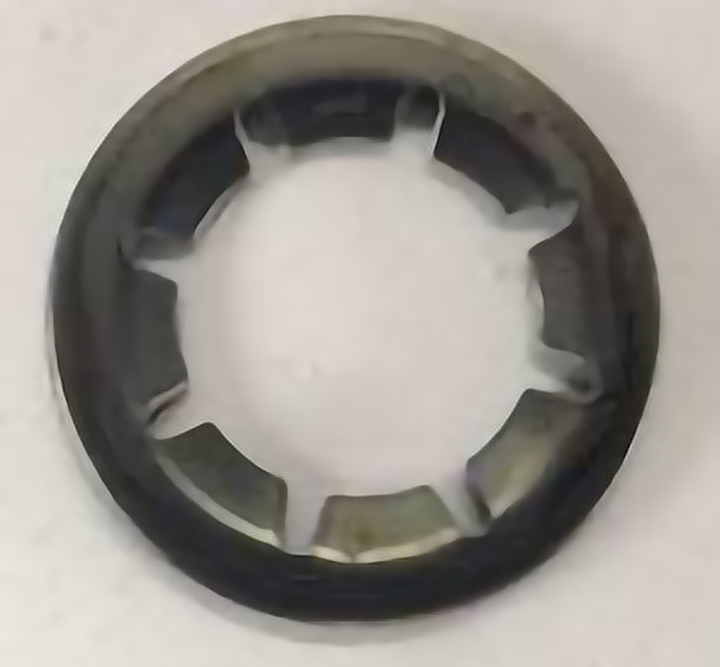
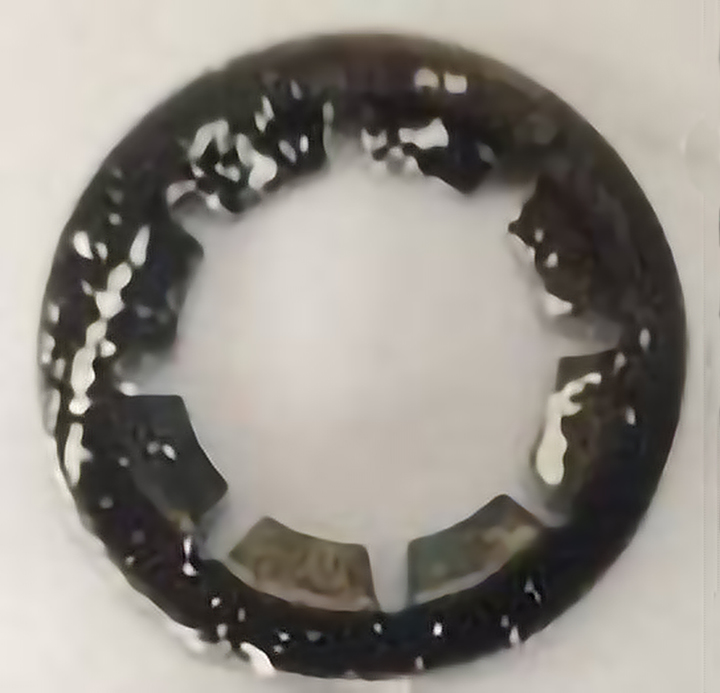
Ein weißes, fusselfreies Tuch wird hierbei über die Oberfläche gerieben. Sichtbare Rückstände auf dem Tuch lassen auf eine unreine Oberfläche schließen.
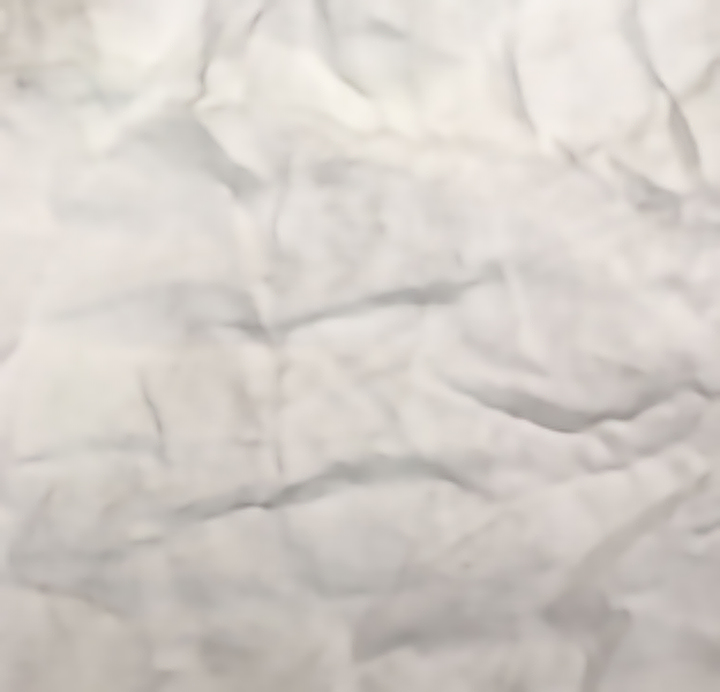
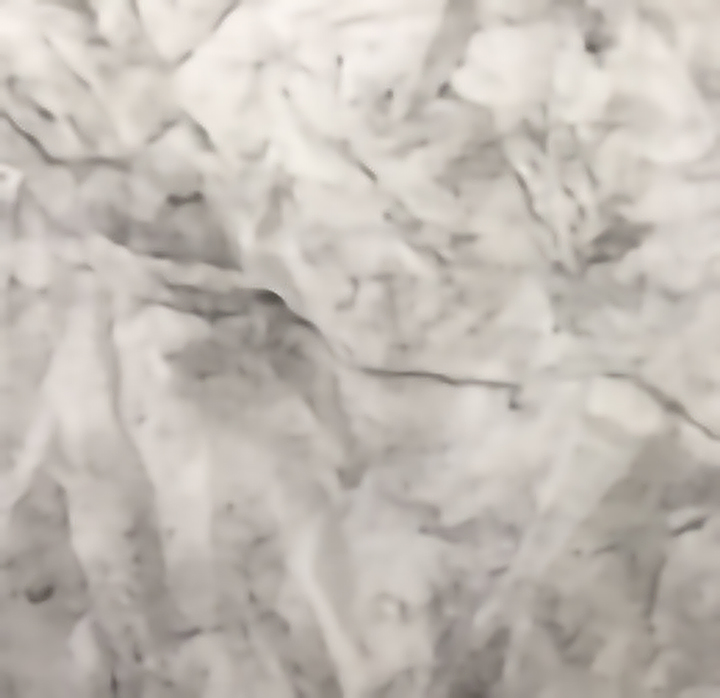
Rückstände wie Öle, Fette, Kühlschmierstoffe etc. können mithilfe eines Verfahrens detektiert werden, bei dem Licht im ultravioletten Bereich mittels einer LED auf einen Messpunkt des Bauteiles emittiert und die Fluoreszenz mit einer Fotodiode gemessen wird. Je höher der Messwert, umso größer die Verschmutzung des Bauteiles.
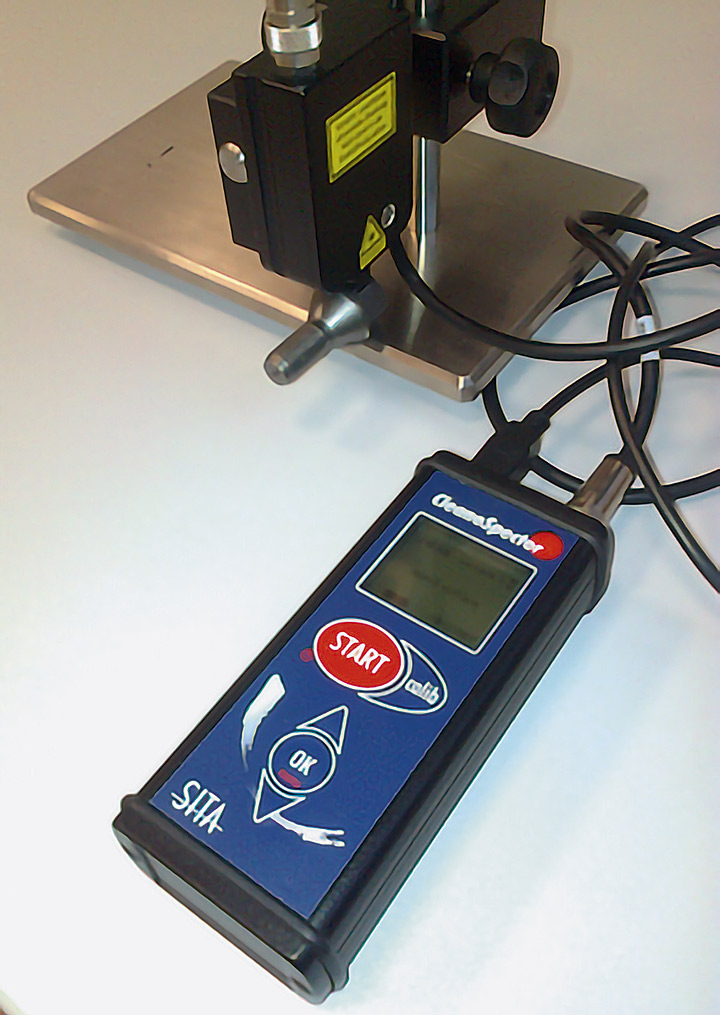
7.2.2 Korrosionsbeständigkeit
Es gibt viele Möglichkeiten, die Korrosionsbeständigkeit zu messen. Meistens wird die Salzsprühnebelprüfung gemäß DIN EN ISO 9227 angewandt, um festzustellen, wie lange es dauert, bis sich Weiß- oder Rotrost bildet.
Für die Durchführung der Salzsprühnebelprüfung benötigt man eine entsprechende Atmosphäre, sodass sich der Einsatz von automatischen Testgeräten empfiehlt. Das Einbringen von Kupfer und Kupferlegierungen in einer Kammer ist zu vermeiden. Eine Liste mit Lieferanten von Messgeräten finden Sie im Anhang A „Lieferanten von Hilfsstoffen und Geräten“.
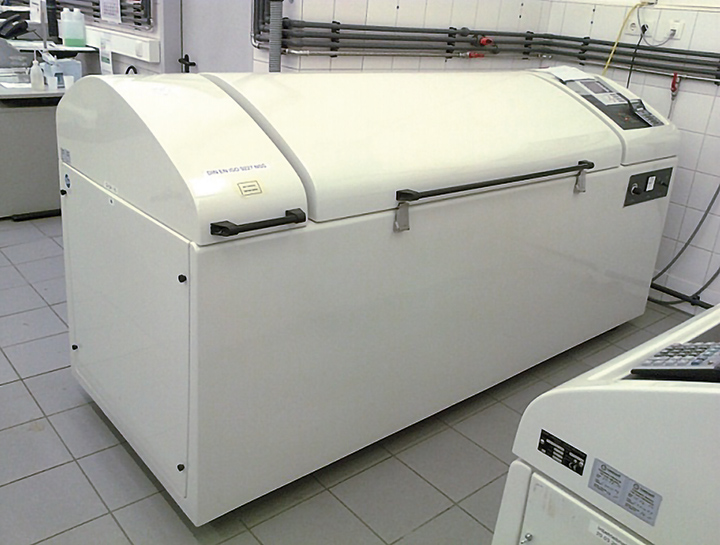
Die Reibungszahl beeinflusst in erheblicher Weise das Verschraubungsverhalten. Von ihr hängt ab, wie viel Drehmoment in Vorspannkraft (die die beiden Bauteile zusammenhält) umgewandelt wird. Eine zu hohe Reibungszahl führt zu niedriger Vorspannkraft und nicht ordnungsgemäß vorgespannter Verbindung. Umgekehrt kann eine zu hohe Vorspannkraft (bei zu niedriger Reibung) zum Abreißen der Schraube führen.
Die mathematischen und prüfungstechnischen Grundlagen sind in der DIN EN ISO 16047 beschrieben. Viele Kunden legen jedoch Wert auf ihre spezifischen Referenzteile (Muttern, Scheiben, Leisten) und die Auswertmethode, da sie unterschiedlichen Ergebnisse führen können.
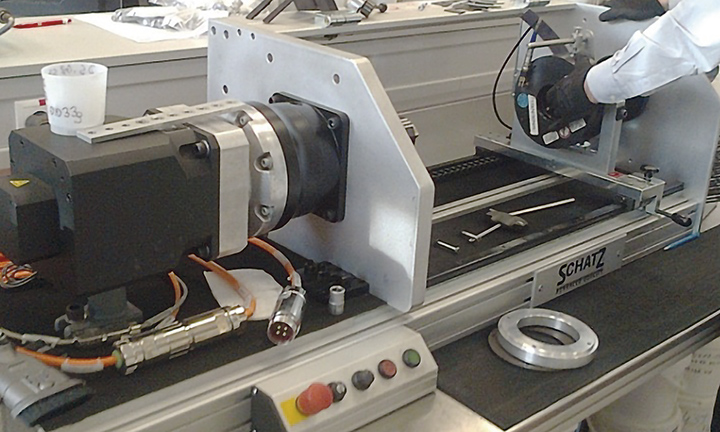
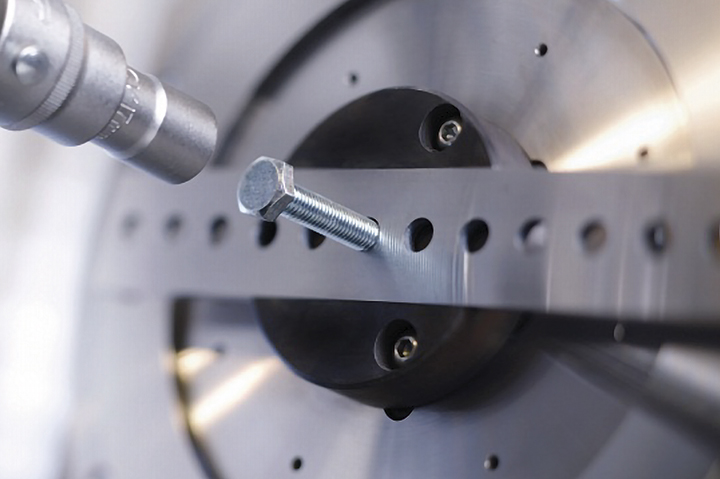
Eine Beschichtung braucht Platz – von daher sind schon bei der Gewindeherstellung die Schichtdicken zu beachten und in entsprechende Toleranzklassen einzuordnen. Die DIN EN ISO 10683 hat diesen Platz in den Toleranzklassen berechnet und grafisch dargestellt in der Dörken Anweisung.
Überprüfung durch die Lehren mit Prüflehren nach DIN EN ISO 1502 (zu beachten sind auch die Schlagstellen/Gewindebeschädigungen nach DIN EN 26157. Die werden mit den gleichen Prüflehren kontrolliert, sodass das Fehlerbild genau zu überprüfen ist).
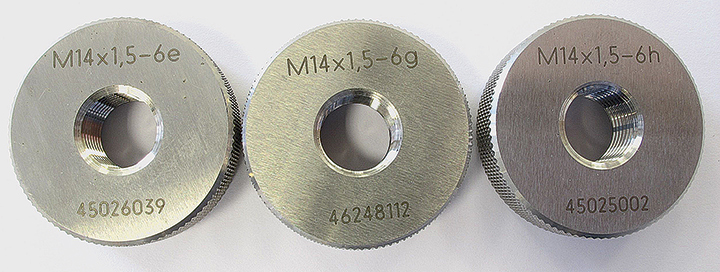
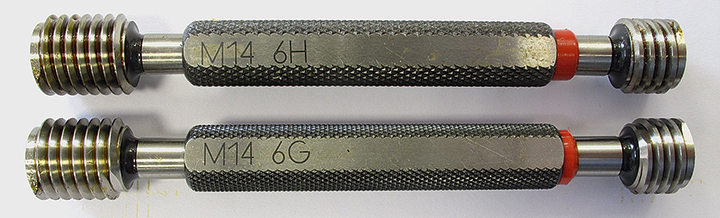

Das durchschnittliche Gewicht der Beschichtung ist sehr einfach zu ermitteln. Hierzu nimmt man eine passende Anzahl von Teilen (z. B. 5 Schrauben) und wiegt sie vor und nach dem Beschichten. Die Differenz ist das Gewicht der Beschichtung für die entsprechende Anzahl der Teile.
Da die Teile selbst Gewichtsunterschiede aufweisen, ist es empfehlenswert, die zum Wiegen verwendeten Teile mit Markierungen zu versehen, die auch nach dem Beschichten erkennbar sind. So kann man dieselben Teile wiegen und sicher sein, dass kein Fehler aufgrund des Eigengewichts der Teile auftritt. Es empfiehlt sich, während des Prozesses Handschuhe zu tragen.
- Hilfsmittel: präzise Waage, Handschuhe
Die Schichtdicke ist sehr gering, da unsere Produkte im Bereich von nur wenigen µm appliziert werden. Dies erschwert die Messung.
Sehr häufig werden elektronische Messgeräte auf Grundlage der Induktion eingesetzt. Es wird eine Sonde mit einem Magnetfeld auf die Oberfläche aufgesetzt. Bei Stahlsubstraten wird das unter dem Lack induzierte Magnetfeld gemessen. Für alle anderen Metalle, die keinen ferromagnetischen Effekt aufweisen (wie Aluminium, Kupfer etc.), wird die Wirbelstromprüfung eingesetzt. In diesen Fällen kann derselbe Aufbau verwendet werden, wobei jedoch die Sonden auszutauschen sind. Der gemessene Wert hängt vom Abstand zwischen Substrat (z. B. Stahl) und Sonde ab. Die Reproduzierbarkeit beträgt in der Regel um die 10%.
Grundsätzlich ist vor jeder Messung eine neue Kalibration durchzuführen. Es sei denn, es ist hierfür eine Applikation hinterlegt (siehe Rückseite Gerät): Dann „Appl No“ drücken, um die Applikation auszuwählen und eine kurze Kontrolle auf dem Grundwerkstoff durchführen. Wenn der Wert um 0 (+/- 2 µm) liegt, kann gemessen werden.
Messung am Beispiel von Fischer MP40:
- Gerät einschalten > betriebsbereit, es kann gemessen werden.
- Für eine Blockauswertung (Mittelwert, STD usw.) einer bestimmten Anzahl an Messungen sollte man mit n=0 starten. Nach fünf Messungen „Block-Res“ drücken. Durch weiteres Drücken gelangt man zu den einzelnen Auswertungen. Dabei sind Abweichungen bis zu +/- 3µm normal.
Wie messe ich richtig?
- Bei Krümmung: Kalibrierung auf der gekrümmten Stelle durchführen. Hilfsstativ und Sondenkeil benutzen.
- Große Messfläche: Bei einem sehr kleinen Prüfteil werden die Kalibrierung und die Messung immer an der gleichen Position gemacht.
- Feldeindringtiefe: Sicherstellen, dass keine Schwankungen der Grundwerkstoffdicke vorliegt. Kalibrierung auf der zu messenden Fläche durchführen.
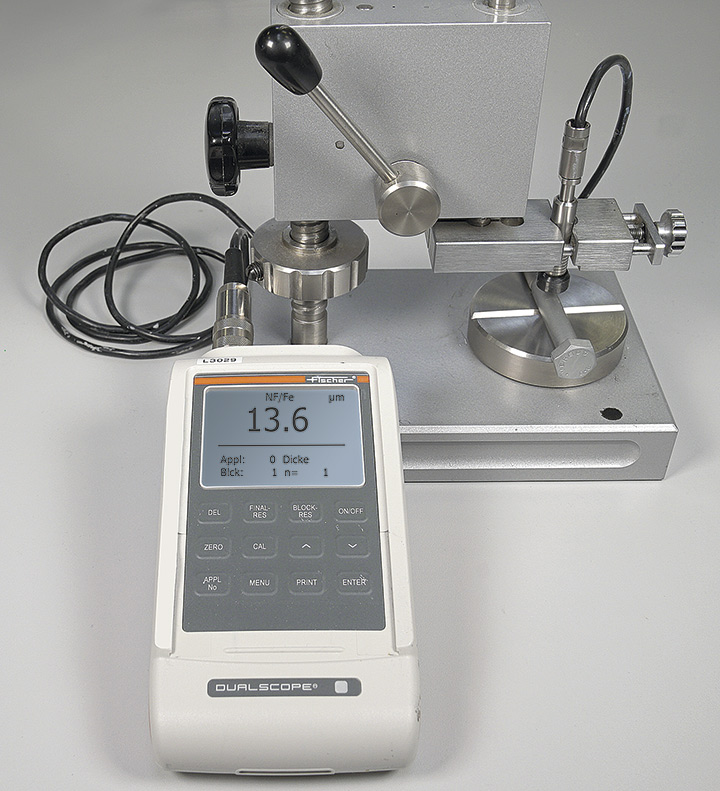
Eine andere Möglichkeit ist die Messung mit Röntgenstrahlung. Das Substrat der Probe sendet nach Anregung charakteristische Röntgenstrahlen aus. Je mehr von diesen Wellen von der Beschichtung absorbiert werden, desto dicker ist die Schicht. Bei angemessener Kalibrierung gibt das Messgerät die Schichtdicke aus. Mit dieser Messmethode können nur Basecoats bestimmt werden. Korrekturfaktoren für die Zinklamellensysteme können gerne angefragt werden.
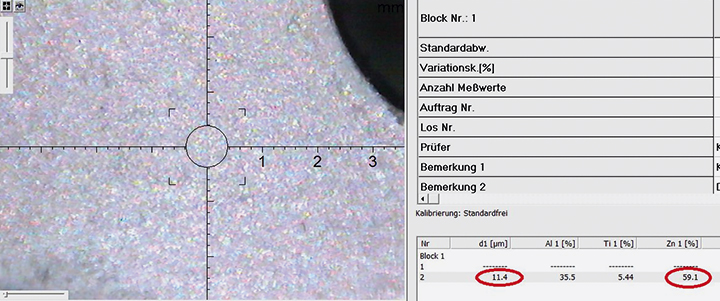
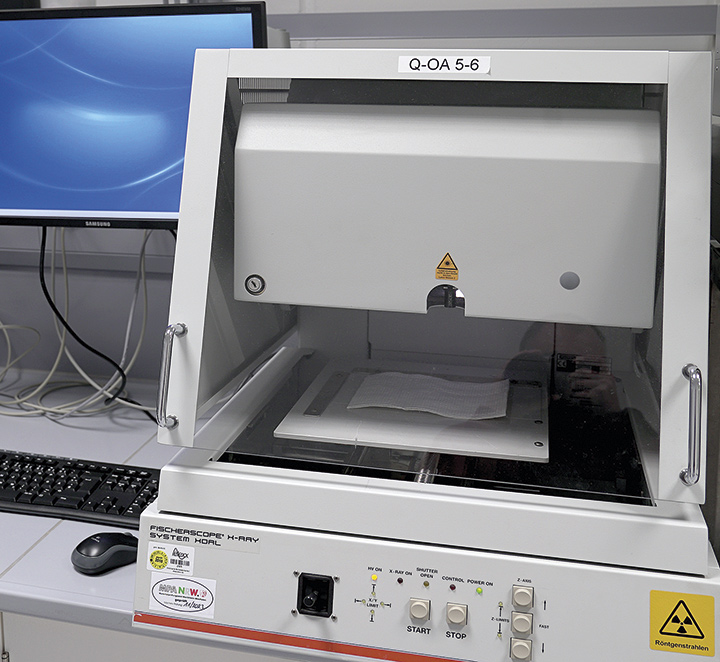
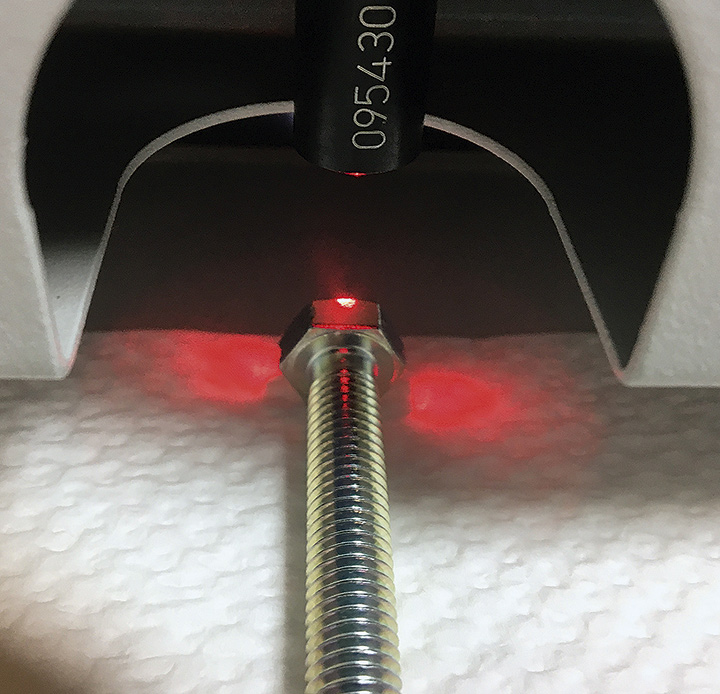
Die präziseste Methode zur Bestimmung der Schichtdicke ist das Anfertigen eines Querschliffes mit anschließender mikroskopischer Auswertung. Im Schiedsfall gilt das in DIN EN ISO 1463 beschriebene mikroskopische Verfahren als Referenzmethode.
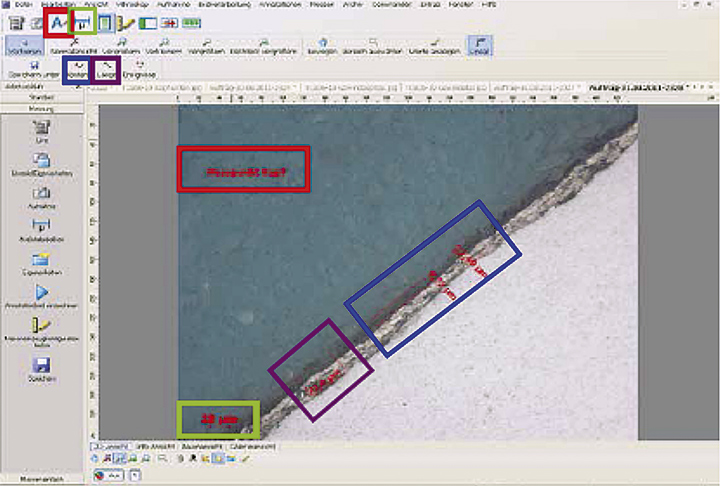
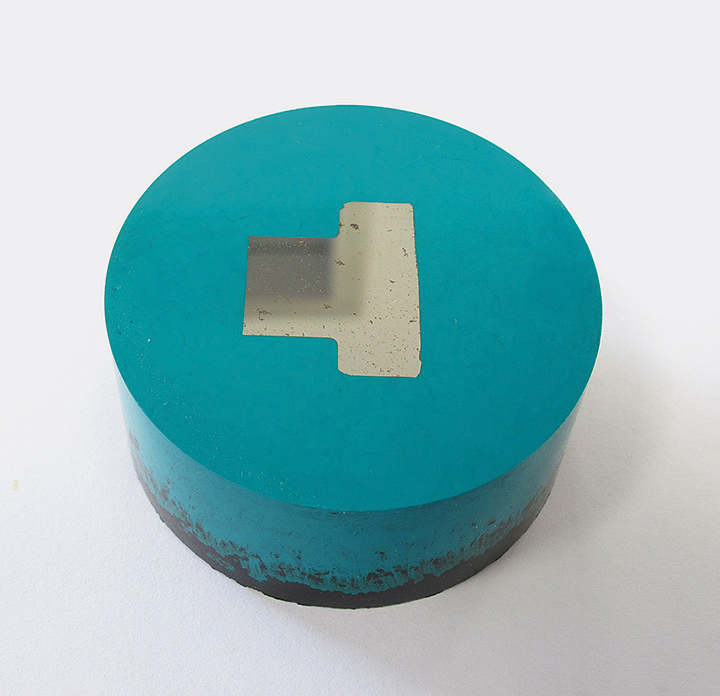
Die Haftfestigkeit wird meist durch einen Klebebandtest geprüft. Manchmal erfolgt sie auch in Verbindung mit einer Gitterschnittprüfung. Das Klebeband wird auf die Probe geklebt, mit den Fingern bzw. einem Radiergummi fest gerieben und dann ruckartig abgezogen, um zu sehen, ob ein Teil der Beschichtung am Klebeband haftet. Da die Anpresskraft, die Geschwindigkeit des Abziehens und die Bewertung, wie viel Lack am Klebeband haftet, nur schwer zu reproduzieren sind, sollte zumindest stets das gleiche Klebeband verwendet werden.
Beim Prüfen der Haftung eines Basecoats sollte sich dieser nicht vollständig vom Substrat lösen, so dass der blanke Stahl zu sehen ist. Kleine Mengen von Metallrückständen auf dem Klebeband sind durchaus normal.
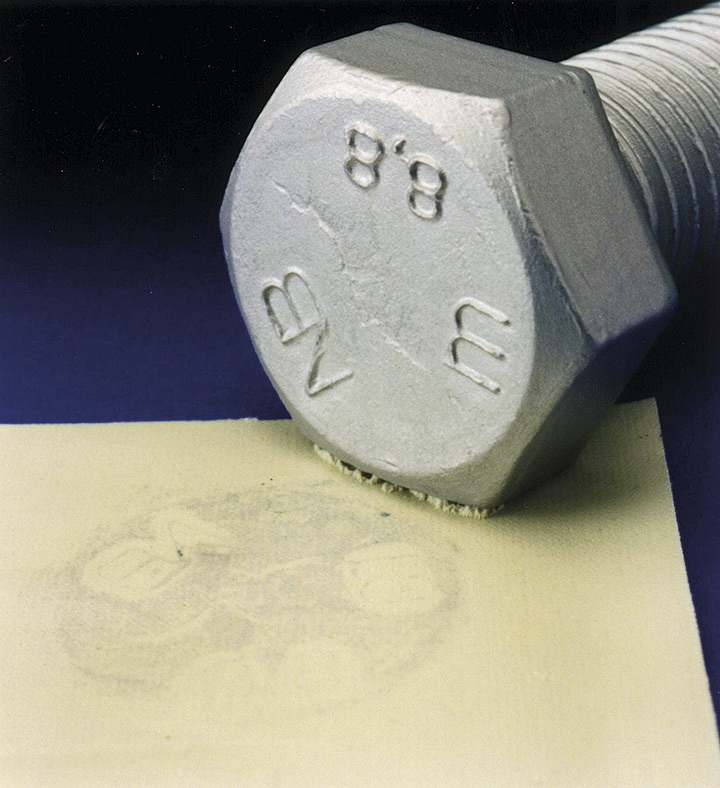
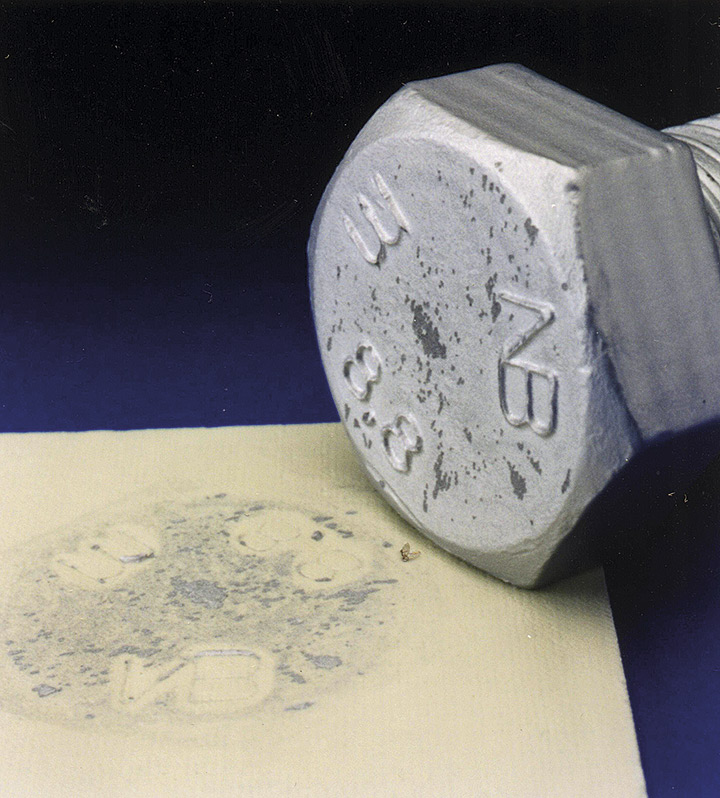
Für die Gitterschnittprüfung sind mit einem scharfen Messer 6 parallele Schnitte und dann dazu 6 senkrecht Schnitte so anzubringen, dass 25 Quadrate entstehen. Eine detaillierte Beschreibung der Gitterschnittprüfung und insbesondere der Bewertung finden Sie in der Norm DIN EN ISO 2409.
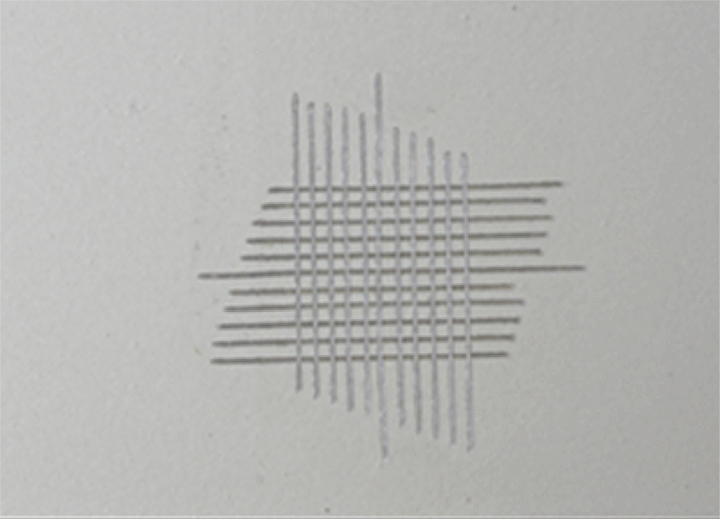
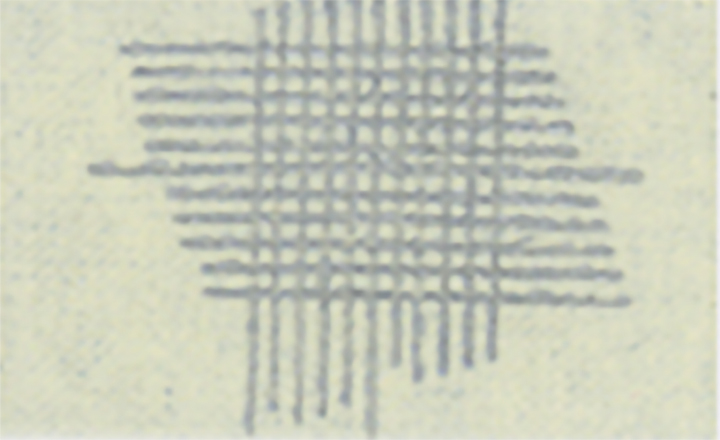
Um zu prüfen, ob ein Topcoat auf einer zinkhaltigen Schicht vorhanden ist, wird eine Kupfersulfatlösung aufgebracht. Bereits nach wenigen Sekunden ist eine mögliche Veränderung sichtbar. Wenn zu wenig oder gar kein Topcoat vorhanden ist, wird sich das Kupfer als braune bis schwarze Sedimentation niederschlagen (siehe Anhang D „Test auf Versiegelung – Verfahren: Tüpfeltest“).
Kommentare (1)
Haben Sie konstruktives Feedback?
Bitte Einloggen um einen Kommentar zu hinterlassen.